Reliability Implementation employs Failure Modes and Effects Analysis (FMEA). FMEA is the is a systematic, proactive method for evaluating how a system or process might fail. This is performed to assess the relative impact of different failures, in order to identify the parts/process that are most in need of change.
Simply put a Failure Mode, Effects & Criticality Analysis (FMECA) is a FMEA with the inclusion of a criticality assessment.
Performing a Design FMEA (DFMEA) or a Functional FMEA will facilitate the development of a more robust system if performed early in the design phase.
Failure Modes and Effects Analysis: Key Elements
The Cameo Systems Modeler FMEA plugin specifies key elements and relationships needed to develop a FMEA and FMECA Table. The following elements and relationships will be used to create a comprehensive FMEA Table.
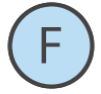
FMEA Item
Identifies the FMEA Item ID.
Failure Mode
An element describing the specific manner in which a component, subsystem, system, process, etc., could potentially fail to meet the design intent.
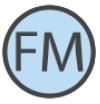
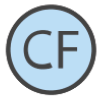
Cause of Failure
Probable reason for the failure mode occurring.
Local Effect of Failure
The consequence of the failure on the item or adjacent items.
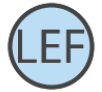
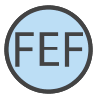
Final Effect of Failure
End effects evaluate and identify the total effect a failure has on the operation, function, or status of the uppermost system or end item and the surrounding
environment.
Prevention Control
A Prevention Control element describes the measures for preventing the occurrence of a possible Failure Mode.
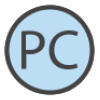
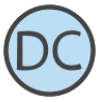
Detection Control
A Detection Control element describes the measures for detecting a Failure Mode, if it occurs.
Failure Modes and Effects Analysis: Key Relationships
Failure Mode Relation
Is a type of dependency relationship relating the Failure Mode (target) to the FMEA Item (Source).
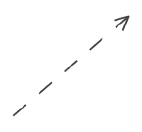
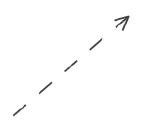
Cause of Failure Relation
Is a type of dependency relationship relating the Cause of Failure (target) to the FMEA Item (Source).
Local Effect of Failure Relation
Is a type of dependency relationship relating the Local Effect of Failure (target) to the FMEA Item (Source).
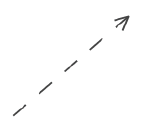
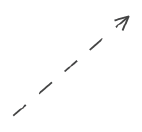
Final Effect of Failure Relation
Is a type of dependency relationship relating the Final Effect of Failure (target) to the FMEA Item (Source).
Prevention Control Relation
Is a type of dependency relationship relating the Prevention Control (target) to the FMEA Item (Source).
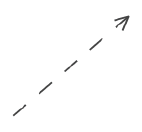
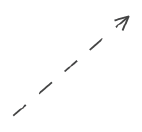
Detection Control Relation
Is a type of dependency relationship relating the Detection Control (target) to the FMEA Item (Source).
Failure Modes and Effects Analysis
Failure Modes and Effects Analysis Process
FMEA Step | Description of FMEA Step |
---|---|
1. Understand Process / Product | Identify the process/product that is being assessed. |
2. Brainstorm Potential Failure Modes | This step focuses on capturing the failures of the assessed process/product. |
3. Identify Effects of Each Failure Mode | Identify if the failure were to occur, what would be the result. |
4. Brainstorm Potential Causes of Failure | Identify what could cause the failure mode to occur. |
5. Apply Failure Mode to Product Behavior | Apply the Failure Mode to Activity that has been captured within the System Model. |
6. Brainstorm Mitigation Controls | Identify the Detection and Protection Controls that could prevent the cause of failure from occurring. |
7. Identify Risk Priority Number (RPN) for Failure Mode | Calculate the RPN by the Occurrence (Cause of Failure), Detectability (Detection Control), and Severity (Final Effect). |
8. Prioritize Failure Modes to Reduce | Rank the Failure Modes that are most critical to fix and reduce their risk. |
Failure Modes & Effects Analysis

Best Practices
When developing a DFMEA/Functional FMEA an identified Failure Mode should be applied to an Activity the system is performing. For comprehensiveness, all functions of the system should have at least 1 Failure Mode associated.
It is best to work with the design agent of the system/component or process undergoing a FMEA assessment.